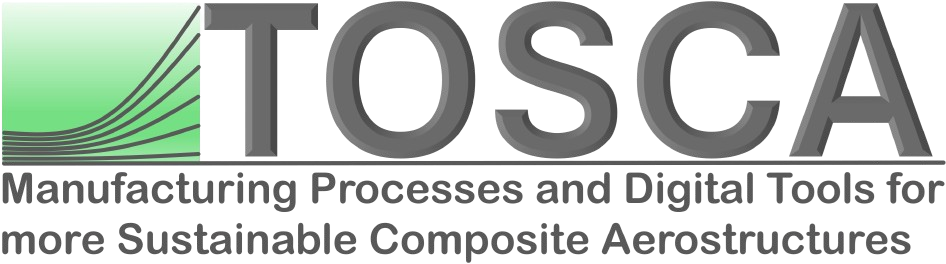
Context
The advantages of lightweight carbon and glass fibre composites in terms of increased fuel efficiency and mechanical performance are now commonly accepted. However, there are persistent economical and technical problems with the recycling of such composites, which are becoming apparent as the first planes with a substantial material fraction of composites are now reaching their end of life. Furthermore, the manufacturing processes are comparably energy- and time-intensive, which creates economic challenges. Progress has already been made in the sector of materials, with new types of thermoplastic and thermoset resins and now is the time to address future manufacturing processes for such materials. The TOSCA project aims to provide key technologies for manufacturing of composite aerostructures in the following areas:
- Epoxy vitrimer resins have shown substantial advantages in terms of repair and recycling, while maintaining almost all the advantages of conventional thermoset resins. However, development is still needed in order to ensure that the processing of such new material is economically competitive.
- There will be an increased need for automation of the documentation of parts “as manufactured” and “as used”. Integrated inspection systems and methods for health monitoring are needed, that will populate data structures for the digitalization of parts.
- Lay-up (mostly automated fibre placement), welding, repair and re-work processes are required for the new materials and these processes also need to take digital information into account coming from the inspection processes aiming at a zero-defect manufacturing approach.
These developments will advance the use of new, sustainable materials, by providing not only the material, but also a set of zero-defect manufacturing technologies that can be used at scale for the manufacturing of future aerostructures. This will avoid some of the current weaknesses in the processing of composite structures along their life cycle.
Objectives
New epoxy vitrimer resins and tapes for structural parts manufacturing
To develop out-of-autoclave processes for new epoxy vitrimer resins with high glass transition temperature aiming at the use of such resins in the manufacturing of carbon fibre tapes for automated fibre placement processes, including finding optimal conditions for curing and fibre placement.
Integrated quality control and structural health monitoring
To implement technologies for quality control, for inline inspection and for structural health monitoring. The data generated by these technologies shall be fed into a digital model of the composite part, enabling its later use for accurate decision-making about the need for re-work or repair. Data will also be merged with process parameters to enable a zero-defect approach.
Economically efficient processes for lay-up, welding, re-work and repair
To develop processes for automated fibre placement, welding, re-work and repair that are optimized for the new type of materials and whose main properties correspond to the needs of large future aerostructures.